- Home
- Blog
- Life Sciences
- Harnessing the Potential of Paligo for Medical Device Manufacturing
Harnessing the Potential of Paligo for Medical Device Manufacturing
Share
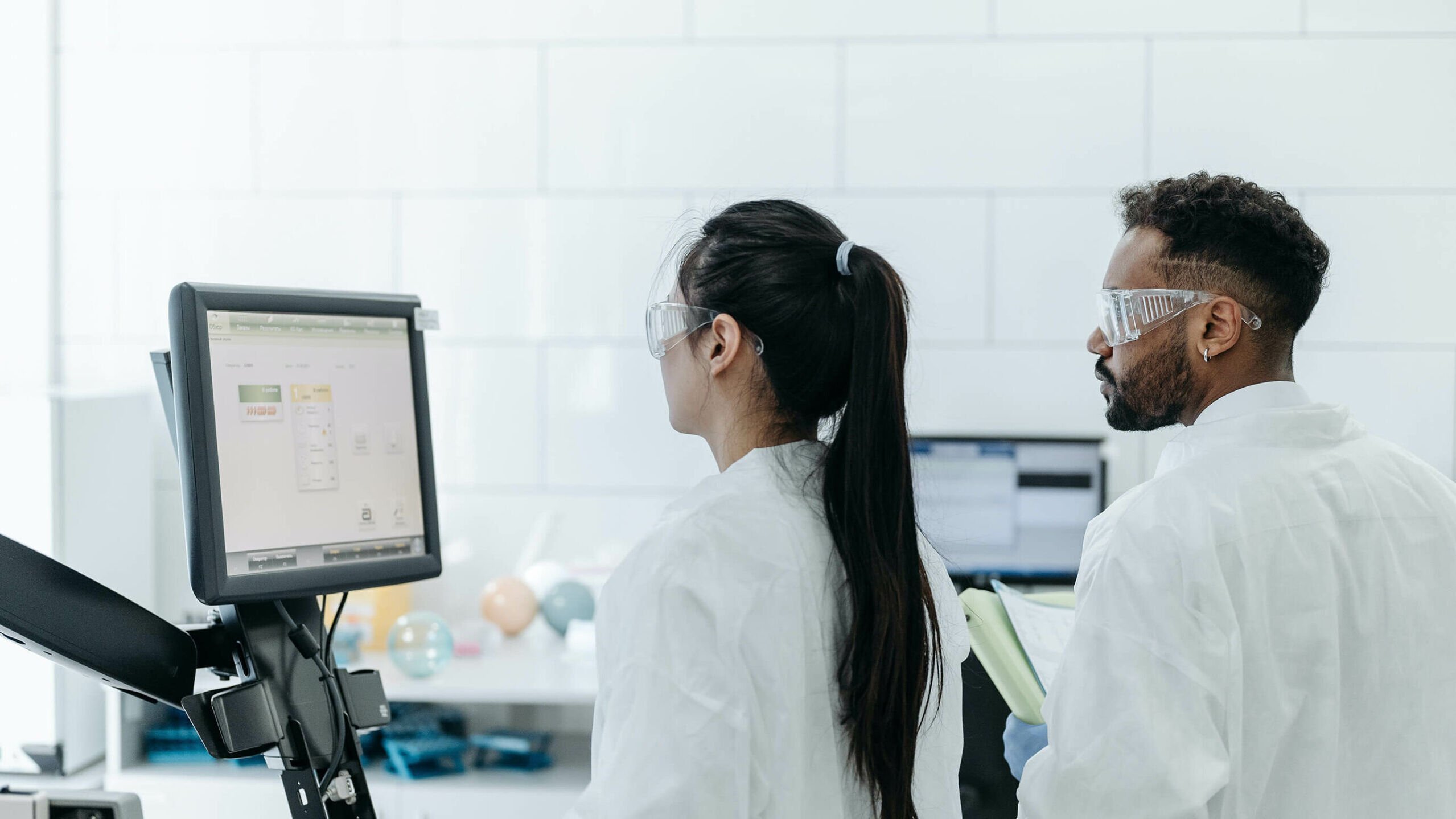
Did you know the medical device industry is a global market expected to grow to $623 billion by 2026? Medical devices come in a variety of shapes and sizes, from hospital beds and elastic bandages for low-risk use to more complex and invasive pieces of equipment like MRIs, pacemakers, and X-ray machines. In fact, the FDA has classified over 1700 devices to date across three risk classes.
It’s a very competitive market and one that is highly regulated. Regardless of who the device is made for (patient, healthcare worker, other) or where it’s used (at home, in a hospital, or in a high-stress environment like the battlefield), these devices must be used correctly to ensure the patient’s safety and the effectiveness of the device. For these reasons and others, accurate and complete technical documentation is critical.
Let’s examine the important technical documentation created for medical devices and consider how a component content management system with structured authoring (like the Paligo CCMS) can help.
Get started with Paligo
Paligo is built to meet the most demanding requirements, with plans made for any company from the growing SMB to the large Enterprise.
Medical Devices Need to Comply with Multiple Regulations
GxP-regulated industries produce a lot of documentation as part of compliance with regulatory agencies, and medical device manufacturing companies are no exception. From product specifications and user manuals to quality control and clinical trial SOPs and other documents, the amount of detailed documentation required to support every device is significant.
Not only is a lot of documentation created, but it’s often in multiple languages and can require lengthy review and approval processes. When you are managing all this documentation using multiple systems, it’s easy to miss things or make mistakes (something you can’t afford to do). It’s not uncommon for regulatory approval to get delayed due to missing, inconsistent, or inaccurate documentation.
The medical device industry is highly regulated. Depending on where a manufacturer sells its products, it may have to comply with regulations from more than one regulatory body. For example, for any device sold in the US, manufacturers must comply with regulations from the FDA (Food and Drug Administration). If they also want to sell their device in the EU, they must follow the European Union Medical Device Regulations (EU MDR). In addition, many countries also have their own regulations. And keep in mind that the more risk a medical device has, the more regulations it must follow. It can get pretty complicated.
Part of the compliance requirements involve the creation of comprehensive product documentation. Typically, medical devices require clear and accurate instructions on how they work and how to use them. This can include instructions for use, labeling on the device, instruction manuals, or user guides. This content supports users, outlining what needs to be done, how it should be done, and when it should be completed. Setup, operation, cleaning and maintenance, alarm and error-message troubleshooting, device specifications, and so on all need to be included. This information must be consistent across all documentation.
Other product documentation, such as advertising and promotional materials, are also subject to regulations, as mislabeling a medical device is a safety issue. By employing a CCMS in your medical documentation, you can provide your medical and technical writers, quality analysts, subject matter experts, and reviewers with an environment that helps them create accurate, reliable, and consistent content. One that enables them to reuse content across documents, supports the creation of documents in multiple languages and helps them get that information in the right hands (and the right format) faster.
Dealing with Different Regulatory Bodies
As mentioned above, medical device manufacturing is subject to many regulations, and these regulations outline the documentation that is required to gain regulatory approval. When you sell your product in multiple countries or regions, you are often required to produce different documentation or have different information in your standard documents.
A CCMS, like Paligo, provides filtering (also known as profiling or conditional content) that enables you to include or exclude content from a document depending on certain conditions. You can filter entire components or elements in a component, like a paragraph or set of steps. So, for example, you must have specific information on your packaging label for the EU that is not required for the United States (US).
Filtering allows you to create one version of a document that includes or excludes certain content depending on who it is published for. There are filtering attributes for product name, audience, market, country, and others.
You can also leverage metadata on topics to do the same thing. In this case, you simply apply your taxonomy to a component (topic) and then filter on profiles that are mapped to the specific taxonomy terms.
Managing the Many Documents of Medical Device Manufacturing
As an industry, pharma is realizing that using a document as the unit of content is cumbersome, costly, and complicated to manage on a large scale. Many are contemplating the move to a Structured Content Authoring environment.
– Val Swisher, Content Rules (Data Not Documents)
When a medical device manufacturing company submits a new medical device for regulatory approval, a lot of documentation is included in the submission process. Specific requirements and documentation may vary depending on the regulatory authority and the type of device or drug, but the amount is still significant.
A few examples:
- Detailed documentation on the device’s manufacturing processes, quality control procedures, and specifications to ensure consistent production and product quality.
- Comprehensive labeling and packaging details, including product labeling, instructions for use, warnings, precautions, and any relevant patient information leaflets.
- User guides, installation guides, field maintenance manuals, and product manuals explain how to install, use, and maintain devices.
It takes time to create all this content, and the review and approval process adds even more time. It’s not uncommon for it to take up to 5x longer to produce content for pharma and medical device manufacturing companies than for other industries.
Here’s where the trouble begins.
Yes, a great deal of documentation is required for regulatory approval, but there is also a lot of similar content between documents. As a result, technical and medical writers do a lot of copying, pasting, or duplicating content across documents. Not only is this inefficient and time-consuming, but it’s risky because errors can happen.
Then there are inconsistencies across documents from revisions, terminology usage, and meaning. These inconsistencies confuse readers and reviewers. They prolong the review process and could cause problems for the end consumer.
What happens when a piece of content needs to be updated? Maybe it’s a section in a document that is used in multiple documents (like a product description or a warning). Authors need to search for every place that content is used and update it manually. If that content is written slightly differently or uses different terminology, it may never be found to get updated, leading to inspection problems. Also, if only one or two sections of a document are updated, the entire document still has to go through the review and approval process, which takes more time and is a redundant effort.
As an example, Paligo works with a company that produces variations of a medical device and needs separate product and installation manuals for each variation. There is a lot of common information between variations, and writers were either cutting and pasting or manually rewriting the same information repeatedly. When a document review required a change in a warning (admonition) used throughout the document or in the other versions, the writer had to manually find and make the changes in each document, affecting the review process for all documents.
What we’ll show you is how this company resolved its content challenges using structured authoring and the Paligo CCMS.
How Structured Authoring Eases Document Management Challenges
You’ve probably heard stories of delayed device approvals because the documentation wasn’t complete or accurate. And you likely have your own horror stories about the efforts required to create the required documentation or keep it updated. But it doesn’t have to be this way. Structured authoring and a component content management system (CCMS) answer these challenges.
When you create your documents using a structured content model, you create and manage content topics (or components) that you can reuse across documents. When a change is made to a topic, every document that includes it is updated. You don’t have to review the entire document, only the updated topic, when a change is made.
Now you might think your writers need to know XML to write structured content. They don’t. When you use the Paligo CCMS, you can easily create and manage reusable content without needing to work directly with XML. Instead, writers focus on creating content, pulling in reusable content components from the library, and writing custom content where necessary. Security is put in place to ensure that only those allowed can access content for reuse and that only approved writers can change reusable components.
If changes are made to a component reused in other documents, those documents are automatically updated. And review and approval is only necessary for the updated component, not the entire document(s). The content is also separated from its styling, so writers don’t need to worry about formatting for different documents or publishing channels.
Localization is another critical aspect of medical device manufacturing documentation. Manufacturers provide their devices to multiple countries and regions, requiring documentation in multiple languages. Different documentation is also required in some instances, or additional information is needed in existing documents. A CCMS fully supports the localization process and manages the publication of translated documents to multiple output formats.
One Place to Manage All Your Technical Documentation
You can create many types of documentation in a CCMS. That documentation may need to be published in different formats, in different locations, or have variations depending on the country or regulatory body.
First of all, CCMS software uses structured authoring, which means that you can create documents in a more organized and structured way. With a structured authoring model, you can create documents with a clear structure and hierarchy, making it easier to find and use the information you need, especially since all content is contained in a single source.
Single-sourcing enables you to create all your documentation in one place and publish it to multiple outputs. For example, many countries, notably in Europe, require you to deliver printed manuals with your devices. Other countries only require digital documentation, and some require both. By single-sourcing your documentation, you can meet all requirements without creating multiple versions of your documentation. The Paligo CCMS supports publishing to HTML5, PDF, CRMs, SCORM, and more.
Also, single-sourcing supports the ability to reuse content created for one type of documentation in another. The most straightforward example is a basic product description that is used in all product documentation, but there are plenty of other examples of content reuse, including instructions, warnings, and visual diagrams.
When you create content using a structured authoring model, you break the structured content into discrete topics that you can reuse in other publications. If you need to change the information – maybe you add a new feature or instruction – you make the change once, and it’s reflected everywhere that information is reused. Updates like this also happen due to changes in standards or regulations. By reusing content, you can make changes swiftly and ensure compliance.
All medical documentation must follow Good Documentation Practices (GDocP). These are guidelines for all forms, records, notes, and other documents produced and documented to meet GMP and other regulatory requirements. Using a CCMS that offers single-sourcing and content reuse, it’s much easier to ensure these guidelines are followed.
Easily Manage and Share Warning and Cautions
Warnings and cautions are critical elements of medical device documentation. The FDA, Health Canada, and the EU MDR all offer guidance on creating these warnings. CCMS software provides the ability to create and manage this type of information in a way that is consistent across all your content.
For example, warnings should be clear, concise, and easily visible within the product documentation, including user manuals, labels, and packaging. You should also use internationally recognized symbols, such as those defined by ISO 15223-1, to enhance comprehension, especially for global markets. Common symbols include those for “Warning,” “Caution,” “Do Not Reuse,” and “Do Not Dispose of in Household Waste.” You can configure the CCMS to use these symbols.
Manage Text and Visual Content in One Place
Another key consideration for using CCMS software to author and manage medical device documentation is support for non-text-based content. User guides, manuals, and instructions often include illustrations, screenshots, and photos. When you manage this type of structured content in a CCMS, you add them as components, so the same version is reused across all technical documentation. This content reuse makes it much easier to deal with updates because you only have to update the image once, and it’s updated everywhere it’s used.
Track Changes and Maintain a Complete Audit in Documentation Software
Another key benefit is versioning in a CCMS. Medical device documentation is updated regularly, either because a change was made to a device, how it works, how it’s used, or there’s a change to the standards or regulations the device adheres to. Versioning enables medical product writers, quality assurance and compliance teams, and others to track the changes made in the documentation software over time. A CCMS also provides a review and approval workflow so that any changes go through a review process before publication.
Managing reviews and approvals can be one of the most time-consuming aspects of creating documentation. For example, before discovering Paligo, one customer used a PDF-centric review tool where reviewers would access a PDF version of the documentation and comment. The author would then need to compare the marked-up PDF with their editable version and make the necessary changes. The updated PDF would then be submitted for review.
Review and approval in the Paligo CCMS is seamless. Subject matter experts can review the documentation directly in the CCMS via a Web browser and apply comments. The author can then go in and accept, edit, or reject the edits. They can also use the comments to ask questions or discuss changes, improving collaboration.
Get started with Paligo
Paligo is built to meet the most demanding requirements, with plans made for any company from the growing SMB to the large Enterprise.
Enable Collaboration with Internal and External Teams
A medical device manufacturer rarely handles all the work involved in designing, developing, and manufacturing a device. More often, there are outside partners who provide parts, contribute to the manufacturing or design process, or help with marketing and selling devices globally.
With multiple partners involved, there needs to be a way to collaborate on documentation, and a CCMS supports that by enabling review and approval processes to include external players. In the CCMS, you can allow partners to review your product documentation and comment on it, ensuring that it’s accurate and up to date.
Technical Documentation is a Critical Component of Medical Devices – Manage it Right with a CCMS
Errors and delays in medical device documentation are costly. Patients can die if instructions are confusing or wrong, and critical products that save lives are slow to get to market because documentation takes too long to create, review and approve, and publish. A CCMS enables manufacturers to reduce these risks by providing a collaborative environment that focuses on efficiency and control.
Too often, documentation like user guides and instructions are an afterthought, left to the end of the manufacturing process. But it’s a critical element of any medical device. Safety and performance relate not only to the device, but to the labeling and instructional materials that go with it. The best component content management system will enable you to author, manage, and publish technical documentation in a way that is efficient and ensures its accuracy, completeness, and compliance is essential. That tool is a component content management system.
If you would like to learn more about how a CCMS can help with life science documentation, read here or schedule a demo.
Originally published June 2023. Updated May 2024
Share
Author
Barb Mosher Zinck
Barb Mosher Zinck is a senior content marketer and marketing technology analyst. She works with a range of clients in the tech market and actively tracks and writes about digital marketing, customer experience and enterprise content management. Barb understands the value of technology and works hard to inform and encourage greater understanding of its role in the enterprise